Российские и зарубежные исследователи в достаточном объеме осветили аспекты влияния основных параметров режима бурения и схем промывки шарошечных долот и лопастных долот, оснащенных резцами PDC, на процесс очистки забоя скважины. В ВНИИБТ, были проведены исследования, которые обосновали наличие трех, отдельно протекающих процессов на забое скважины, таковыми являются: первый – это непосредственно очистка поверхности забоя, второй – это очистка призабойной зоны, третий – это очистка вооружения долота. Исходя из этого, возникает необходимость создания систем промывки буровых долот, которые либо в равной степени повышали эффективность всех трех процессов очистки забоя одновременно, либо делали упор на том процессе, повышение эффективности которого наиболее адекватно в данных условиях, либо возникает необходимость улучшить уровень эффективности того процесса, который протекает с наибольшими затруднениями.[1]
Как известно, главная причина снижения эффективности бурения – это рост дифференциального давления с ростом глубины. Данное явление приводит к увеличению силы, прижимающей частицы породы к забою, что затрудняет их отрыв и, следовательно, очистку забоя в целом. При высоких дифференциальных давлениях и низких скоростях фильтрации бурового раствора осуществляется переход к состоянию горных пород, в котором наблюдается псевдопластичное разрушение, вне зависимости от того, каковы прочностные характеристики горных пород в атмосферных условиях. При таких сложных условиях возникает необходимость в присутствии мощного струйного воздействия на забой скважины, что могут обеспечить лишь те гидромониторные насадки, перепад давления в которых достаточно высок. Доказано, что поперечные потоки, возникающие при разрушении струи, исходящей из насадки долота, способствуют увеличению способности частиц разбуренной породы лучше отрываться от забоя. Это вызвано динамическим воздействием гидромониторных струй на периферийную зону забоя, а центральная часть забоя оказывается без воздействия ударной волны. Чтобы усилить эффективность воздействия на разрушенные частицы разбуренной породы, расположенные на забое, используя поперечные потоки промывочной жидкости, можно использовать два способа. Первым способом является распределение воздействия струй жидкости равномерно по всей площади забоя. Второй способ реализуется за счет повышения скоростей истечения жидкости из гидромониторных насадок, так как одним из наиболее важных факторов, определяющих эффективность гидромониторных долот, является скорость истечения, а не расход жидкости.[2]
Несмотря на то, что гидромониторная схема промывки является наиболее распространенной, существуют некоторые недостатки данной схемы промывки буровых долот.
Так как воздействие струй жидкости в гидромониторных долотах направлено на периферийную зону забоя, которая составляет обычно одну треть от площади забоя, промывочное воздействие на центральную часть забоя снижено, что снижает эффективность очистки этой зоны. В центральной зоне забоя происходит хаотичное движение шлама, что приводит к повторному перемалыванию частиц, что снижает эффективность бурения в целом, а в случае шарошечного долота это приводит к попаданию частиц шлама в зазор между спинкой лапы долота и стенкой скважины, что приводит к ускоренному абразивному износу долота.[3]
Имеет место факт воздействия струй не только на поверхность забоя, но и на стенки скважины в некоторых типах конструкций буровых долот. Ориентация струй бурового раствора обычно обуславливает попадание оси струи в 12-14 мм от стенки скважины. Так как конус рассеивания струи обычно составляет до 3 dn, наблюдается непосредственное воздействие части струи на стенку скважины. Данное явление отрицательно воздействует на эффективность бурения в мягких и пластичных породах. В такой ситуации имеется повышенное струйное воздействие на породу и повышенное вихреобразование бурового раствора в призабойной зоне скважины, которые приводят к значительному увеличению кавернообразования ствола скважины.[4]
Кроме того, обычно происходит очистка только периферийной части долота, что снижает агрессивность вооружения долота. Такое явление наблюдается в основном в глинистых породах, как следствие, снижается эффективность процесса разрушения горной породы. Основным способом очистки долота от сальников является образование завихрений промывочной жидкости у долота, что обычно оказывается не вполне достаточным.[5]
Для устранения всех перечисленных выше недостатков, которые присущи гидромониторной схеме промывки, было разработано новшество, получившее название – ориентированная система промывки. Для того чтобы внедрить данную систему в область практического применения, было предложено несколько вариантов конструкций промывочных узлов. Данные решения воплощались с помощью наклонных насадок, которые были изготовлены из стали 40Х, которые в дальнейшем подвергались термической обработке. Крепление данных устройств в промывочном канале долота осуществлялось при помощи электродуговой сварки. При пробном вводе в эксплуатацию идеи ориентированной схемы промывки данная система была апробирована. Экспериментальная схема обеспечила прирост скорости проходки в течение первых 3-4 часов работы долота на забое, во время которых велись замеры. За всё долбление не было сильного прироста механической скорости и проходки, а в некоторых случаях наблюдалось даже снижение этих показателей.[6] Причина была в падении скорости истечения жидкости с 70-75 м/с до 40-50 м/с, что происходило из-за чрезмерного эрозионного размыва отверстий промывочных устройств. Характер изменения скорости истечения бурового раствора из насадок в течение долбления представлен на рис. 1.
Для того чтобы имелась возможность осуществлять замену насадок в условиях буровых, были предложены конструкции крепления насадок, изображенные на рис. 2, 3.[10]
Для снижения эжекционного действия истекающих струй и усиления их ударного воздействия на преграду наклонные насадки были приближены к забою на 15-17 мм, что позволило разместить наклонный срез насадок на расстоянии 10-12 мм от зубьев шарошек.[7]
Несмотря на это нововведение должного повышения стойкости насадок к размыву не наблюдалось. Размыв был осуществлен в течение одного долбления.
Для решения данной проблемы была использована минералокерамика 22ХС, как заменитель стали 40Х, применявшейся до этого. Конструкция насадок и узлы их крепления изображены на рис. 2, 3. Несмотря на это, после отработки долот наблюдались случаи слома наклонных насадок с большим углом отклонения, это обусловливалось наличием уступов в кавернозных интервалах наклонно-направленных скважин. Этот эффект наблюдался, в основном, в скважинах с наклоном ствола более 20°.[8]
В целях повышения износостойкости промывочных узлов долот при введении ориентированной схемы промывки возможны следующие конструктивные решения:
1. Замена материала сталь 40Х, из которого ранее изготавливались насадки, на вольфрам карбидовый сплав, такой как, ВК-8, при этом будут сохранены конструкции промывочных узлов, т.е. аналогично тем, что изображены на рис.2, 3.
2. Применение обычных насадок минимально возможных высот, которые необходимо устанавливать в оправке (стаканчике) крепления под определенным углом к оси промывочного канала (рис.4).
Главное достоинство данной конструкции – это возможность применения в серийных гидромониторных долотах, а также установка насадок под нужным углом к оси долота. Главный недостаток – высокая сложность в изготовлении.
3. Изменение направления действия истекающих струй жидкости с помощью изменения конструктивной ориентации в нужном направлении самих промывочных каналов. Предложенная конструкция лишена недостатка прошлой системы, но и обеспечивает более эффективное удаление частиц шлама из призабойной зоны благодаря перемещению промывочных узлов ближе к оси долота, и как следствие этого, имеет место увеличение "живого" сечения для восходящих потоков жидкости.[9]
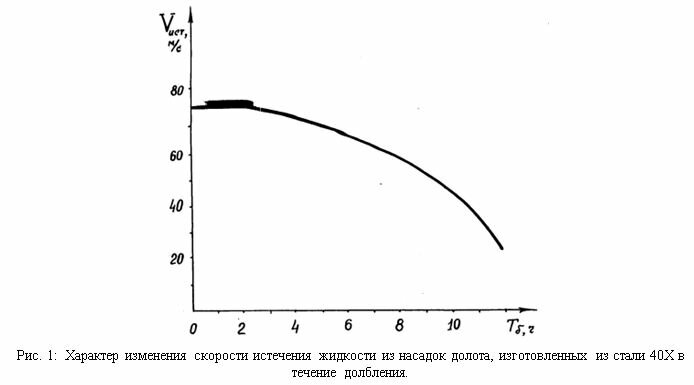
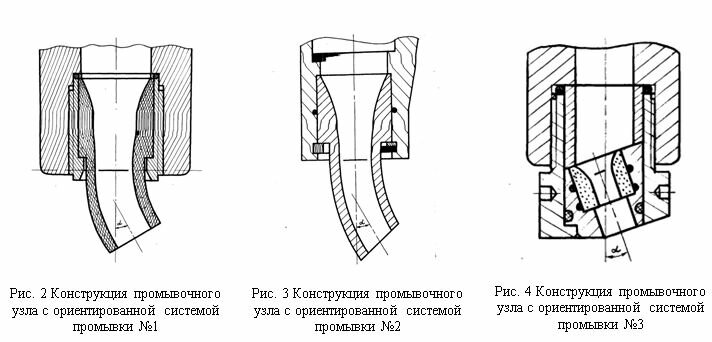
Резюмируя вышесказанное можно сделать следующие выводы:
1. Ориентированная схема промывки повышает эффективность каждого из трех частных процессов очистки забоя скважины, необходимость поддержания которых на высоком уровне возникает в процессе бурения всего разреза скважины;
2. Данная система показала свое превосходство в сравнении с стандартной гидромониторной схемой промывки забоя во всех интервалах бурения, вне зависимости от физико-механических свойств слагающих пород.
3. Данная схема промывки наиболее благоприятна для работы опор шарошечных долот.
4. При использовании данной системы происходит стабилизация параметров кривизны ствола скважины, кроме того уменьшается интенсивность кавернообразования при бурении в интервале залегания глинистых пород.[10]
Литература
1. Адлер Ю.П., Маркова Е.В Планирование эксперимента при поиске оптимальных условий. - М.: Наука, 1976, – 279с.
2. Акопов Э.А. Очистка забоев глубоких скважин» - М.:Недра,1970. – с. 3-13.
3. Айриянц А.С., Симонов В.В., Шацов Н.И. О дроблении шлама между корпусом шарошечного долота и стенками скважины*- Нефть и газ, 1965, – с. 37-41..
4. Буров В. И., Кононцов А.И., Крист М.О., Малкин И.Б. и др. Некоторые результаты опытного бурения скважин гидромониторными долотами при повышенных перепадах давлений на Самотлорском месторождении. - Нефтяное хозяйство, 1973, – с.77-80.
5. Гусман A.M., Малкин И.Б., Мительман Б.И. Исследование эффек¬тивности гидромониторных долот ВНИИБТ, 1970, – с. 119-120.
6. Козодой А.К., Зубарев А.В., Федоров B.C. Промывка скважин при бурении.- М, Гостоптехиздат, 1963. – с. 109-111.
7. Козодой А.К., Варламов ЕЛ. Количественная оценка силового воздействия гидромониторной струи на забой скважины.- Труды ВолгоградНИПИнефгь, 1975, – с. 28-30.
8. Мительман Б,И,, Гусман A.M., Гольдштейн И.Е., Энгель А.С. Исследование эффективности работы гидромониторных долот,- Бурение, 1967, » – 50 с.
9. Соболевский В.В., Шевченко Ю.М., Мясников Б.И. Разрушение горных пород высокоскоростными струями жидкости. - Нефтяное хо¬зяйство, 1974, – с.247-249.
10. Пестров А. П. Разработка рациональных схем промывочных устройств трёхшарошечных долот для бурения скважин в условиях Западной Сибири, 1984, с.117-128.
Работу предоставил: Гребенников А.А.
Научный руководитель: старший преподаватель Баркалов Н.А.