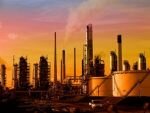
Одним из определяющих факторов развития и процветания любой нефтегазовой компании является своевременное внедрение в производство инновационных технологий для добычи и эффективного использования углеводородного сырья. Развитие нефтегазового сектора, особенно в нашей стране, является наиболее важной задачей, так как большую часть налогов платят именно представители топливно – энергетического комплекса. Поэтому повышение эффективности использования топливно-энергетических ресурсов является наиболее приоритетной задачей для государства, которая была сформулирована еще в 2010 году. В нее входили такие пункты, как: содействие инновационному развитию топливно-энергетического комплекса и совершенствование технологий добычи, транспортировки и повышение глубины переработки углеводородного сырья.
Российская Федерация располагает огромными запасами энергетических ресурсов и мощным топливно-энергетическим комплексом, который является основным для развития экономики, способствует усилению геополитического влияния страны и во многом определяет формирование основных финансово-экономических показателей.
Цель: Рассмотреть повышение эффективности добычи и использования углеводородного сырья на базе инновационных технологий.
Задачи:
- Рассмотреть инновационные технологии в нефтегазовом секторе.
- Сделать выводы о эффективности внедрения инновационных технологий.
2 Инновационные технологии в добыче углеводородов
Значительные запасы углеводородов заставляют все шире применять новые технологии, оборудование, различные системы эксплуатации нефтеносных горизонтов. Главная задача – эффективное и повсеместное внедрение инновационных технологий в производство.
2.1.Бурение с использованием гибких насосно-компрессорных труб (ГНКТ)
Использование гибких НКТ с забойными гидротурбинными двигателями для вращения долота при углублении ствола скважины. Операции бурения с использованием ГНКТ выполняются быстро по сравнению с использованием составных ГНКТ, поскольку исключается время на соединение труб между спусками. Бурение с использованием ГНКТ является экономически эффективным в целом ряде случаев применения, таких как бурение скважин с более тонким стволом, бурение на участках, где существенную роль играет размер площади основания БУ, при повторном входе в скважины и бурении на депрессии.
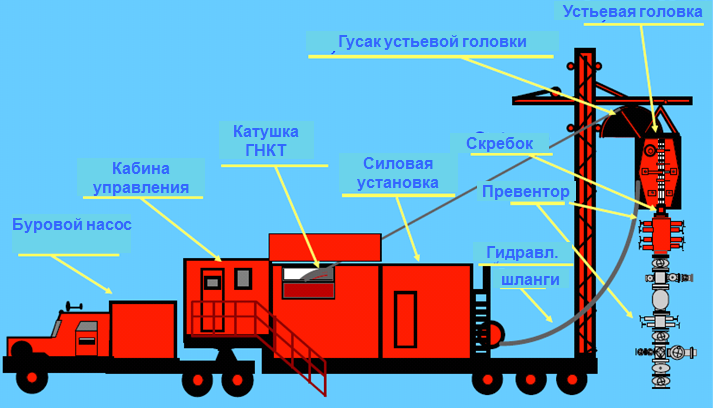
Рисунок 1. Система с ГНКТ
Преимущества гибких НКТ:
- Более быстрый спуск трубы
- Бурение на депрессии
– Легче развернуть буровую колонну под давлением
– Дебит во время бурения и СПО
- Сочетаемость со сжимаемой жидкостью
- Оперативная переброска и монтаж БУ
- Потенциально более низкие затраты
- Полный контроль скважинного давления – выбросы не представляют проблемы
- ЗБС в существующих скважинах
– Бурение через НКТ исключает извлечение трубы
– Использование существующего фонда скважин и инфраструктуры
- Снижение экологического воздействия
– Меньшие по размеру кусты/меньшие площади установки
– Меньше шлама из скважины более мелкого размера
- Исключается НКТ – один из основных источников аварий
- Перспектива сокращения численности персонала и вспомогательного оборудования
Технические ограничения при бурении с использованием ГНКТ:
- Невозможность вращать буровую трубу
– Увеличивается статическое трение
– Уменьшается потенциальная длина скважины (нефтенасыщенная зона)
– Уменьшается возможность прочистки скважины
- Ограниченная прочность труб по сравнению с обычными колоннами
- Ограниченные расходы насосов и размеры скважин
- Ограниченный вес на долоте (вопросы передачи веса)
– Винтовая блокировка
- Срок службы ГНКТ (усталость из-за циклического изменения давления и спусковых операций)
- Более извилистая траектория из-за ограничения, при котором допускается только скольжение при бурении
Технологии, применяемые с использованием гибких НКТ:
1)PowerCLEAN
PowerCLEAN – это комплексная система эффективной и качественной промывки забоя скважин. Эта новая интегрированная система PowerCLEAN позволяет оптимизировать параметры промывки скважин с использованием ГНКТ и обеспечивает высокоэффективное удаление различных типов отложений, включая проппант, пластовый песок и бокситовые отложения.
Система включает в себя:
- программное обеспечение для проектирования работ;
- промывочную форсунку, существенно улучшающую качество промывки;
- специальный состав жидкостей;
- систему мониторинга твердых частиц
2) HPHT Coiled Tubing
HPHT Coiled Tubing представляет собой набор оборудования для работы в условиях высоких температур и давлений, в частности ГНКТ, рассчитанную на работу на скважинах высокого давления, а также дополнительное оборудование для контроля этих скважин. Использование технологии HPHT Coiled Tubing позволяет проводить работы на скважинах высокого давления без последующего глушения скважин.
Преимуществами данного типа ГНКТ являются возможность работать без потери продуктивности скважины и значительное сокращение времени проведения работ.
С данным оборудованием работы могут проводиться на скважинах с максимальным потенциальным давлением на устье до 1000атм. и глубиной более 7000 м. Для работ может быть использовано как наземное, так и оффшорное оборудование.
3) CoilFLATE
Технология CoilFLATE HPHT – это надежный монопосадочный пакер, используемый для изоляции во время стимуляции резервуара, а также других скважинных операций.
CoilFLATE может быть использован в различных целях, например, как пакер для селективной обработки при кислотной обработке, как мостовая пробка для изоляции нижних зон, как цементировочный пакер с обратным клапаном, где несколько типов цемента могут быть закачаны через пакер и под пакер для контролирования воды и песка.
Пакер обеспечивает оптимальную изоляцию и посадку даже при большой разнице давлений. Работы могут быть проведены на скважинах с размерами обсадной колонны до 193.6 мм
[29.7 дюймов] и при температуре до 192
оС.
Технология CoilFLATE ST обеспечивает высокое качество изоляции узконаправленного действия.
Данная технология дает возможность точного контроля глубины, что особенно важно при посадке пакера в районе перфорации. За одну спускоподъемную операцию можно проводить до 10 посадок пакера.
4) Downhole Sensor Package 2
DownholeSensorPackage 2, или комплект забойных датчиков, представляет собой систему, которая позволяет получать точные измерения для оптимизации операций с использованием ГНКТ. DSP2 включает в себя набор оборудования, применимый для разных видов работ с ГНКТ, в частности для получения данных о корреляции глубины и геофизических параметрах в режиме реального времени.
DSP2 позволяет проводить следующие измерения в режиме реального времени:
- внутреннее и внешнее давление,
- температура в данной позиции,
- точная глубина оборудования, основанная на данных локатора обсадной колонны (casing collarlocator).
Оборудование используется с электрическими и фиброоптическими датчиками.
Одной из уникальных применения DSP2 является возможность получения профиля распределения температуры по всей длине скважины. Эти данные сравнимы с измерениями, получаемыми с помощью PLT, где площадь притока из скважины устанавливается достаточно просто, а вероятность ошибки при считывании данных с зон поперечного потока снижается.
5) DepthLOG
DepthLOG – это инновационная технология, позволяющая получать геофизические данные в режиме реального времени в течение каждой работы.
DepthLOG обеспечивает точные результаты по измерению глубины в режиме реального времени. Заказчик получает возможность проведения работы с использованием ГНКТ без дополнительных спуско-подъемных операций геофизического оборудования и связанных с этим затрат.
DepthLOG позволяет получать точные корреляции глубины в режиме реального времени, снижая затраты по сравнению с классическими методами корреляции. Данная технология обеспечивает увеличение количества спуско-подъемных операций, повторяемость измерений, а также геофизические исследования в соответствии со стандартами API.
2.2.Инновация в ГРП
ГРП проводится с целью решения проблемы глубокого повреждения призабойной зоны путём создания трещины высокой проводимости для восстановления контакта скважины с неповреждённой породой.
ГРП повышает производительность скважины, уменьшает период эксплуатации, снижает сумму производственных затраты и улучшает экономические аспекты разработки месторождения.
Эффективность ГРП зависит от:
- Геометрии трещины, т.е. от его длины (xf) и ширины (wf)
- Проницаемости резервуара (k)
- Проницаемости трещины (kf)
Можно также говорить о том, что:
- В резервуарах с низкой проницаемостью
большей эффективности ГРП можно добиться путём
увеличения длины трещины
- В резервуарах с лучшей проницаемостью большая
эффективность ГРП получается за счёт проведения ГРП
меньшей длины, но большей ширины.
На рисунке 2 изображенны новые технологии и различные добавки для более эффективного проведения ГРП, рассмотрим некоторые из них:
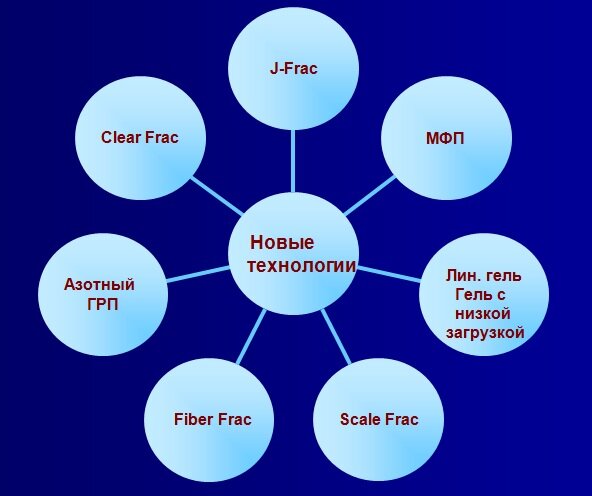
Рисунок 2 Новые технологии в ГРП
1)ГРП с применением азота:
Область применения:
- Пласты с посаженными давлениями
- Пласты чувствительные к воде
- Пласты, находящиеся между водоносными горизонтами
Преимущества:
- Низкое содержание полимера в пласте
- Увеличение длины трещины
- Быстрая очистка скважины от жидкости ГРП
- Увеличение проводимости трещины
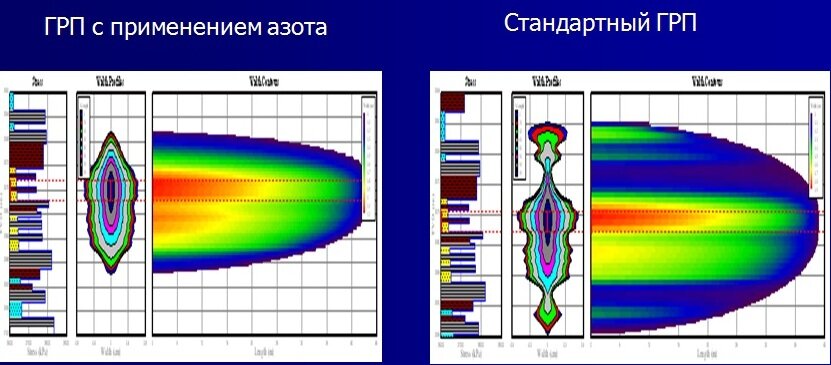
Рисунок 3 Разница в геометрии трещин
Инертность азота, может использоваться с любыми жидкостями
2)Технология Clear-FRAC
Безполимерная система на основе воды состоится из ВПАВ (вязко-упругих поверхностно активных веществ)
Вязкость жидкости два раза меньше чем вязкость стандартного геля на основе гуар/HPG - до 150 cП.
Преимущества:
- Отсутствие полимера означает отсутствие загрязнения
- Максимальная эффективная полудлина трещины и её проницаемость
- Ограничение роста трещины по высоте
- Отсутствие фильтрационной корки
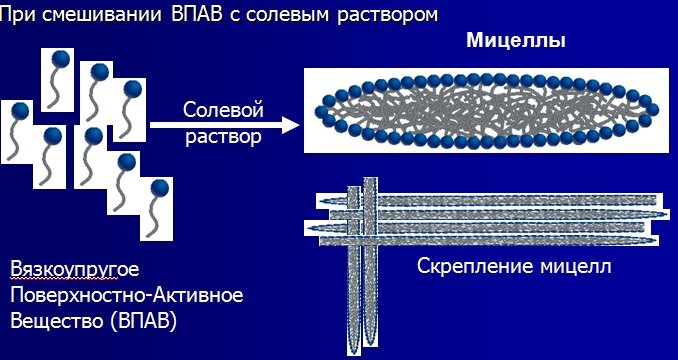
Рисунок 4 Образование Clear -Frac
Разрушение мицеллы наступает при:
При взаимодействии с углеводородами и при растворении с формационными водами
1)Модификаторы фазовой проницаемости (МФП)
Суть технологии:
Применяется в коллекторах с небольшими глинистыми перемычками или отсутствием таковых.
Еще несколько лет назад скважины с высоким риском увеличения обводненности продукции не рассматривались в качестве кандидатов на проведение ГРП
Свойства модификаторов:
- Совместимость с большинством химических добавок
- Широкий температурный диапазон – эффективность
действия при температурах до 121
оС
- Широкий диапазон концентраций – при использовании
содержание МФП в воде может варьироваться от 3%
до 12% в зависимости от проницаемости пласта
- Легкость смешивания – МФП удобны для
транспортировки и легко растворяются в воде
- МФП реагирует с водой, образуя прочные водородные связи с молекулами воды и создавая гидравлическое сопротивление в каналах притока флюидов в скважину
- Это приводит к уменьшению притока воды и увеличению величины давления, необходимого для продавливания воды через поры
- Вместе с тем, возможно некоторое снижение проницаемости для углеводородов, поскольку полимер МФП будет заполнять поровое пространство породы
- При успешной обработке с применением МФП проницаемость породы для воды снижается больше, чем для углеводородов
Помимо новых технологий приведенных на рисунке 2, на практике широко внедряются технологии ГРП с концевым экранированием трещины, ГРП с предварительной гидропескоструйной перфорацией, а так же направленный гидравлический разрыв пласта. Рассмотрим их поподробнее.
1)Технология гидравлического разрыва пласта с концевым экранированием трещины:
Одной из новых эффективных технологий ГРП является технология осаждения проппоната на конце трещин или концевое экранирование трещины, которая позволяет целенаправленно увеличить ширину трещины, останавливает ее рост в длину, за счет чего значительно увеличивается проводимость.
Для предупреждения выноса проппаната из трещины создана технология PropNET, в которой предусматривается закачка в пласт одновременно с проппанатом специального гибкого стекловолокна, которое, заполняя промежутки частицами проппоната, обеспечивает максимальную устойчивость проппонатной пачки. Разработаны и применяются низкополимерные жидкости разрыва LOWGuar и система добавок деструктора Clean FLOW для снижения остаточного загрязнения трещин.
Наибольшее распространение имеет локальный гидроразрыв для снижения сопротивления призабойной зоны и увеличения эффективного радиуса скважины. Для высокопроницаемых коллекторов главным фактором увеличения производительности скважин является ширина трещин, а низкопроницаемых - длина трещины. Для создания широких трещин применяется технология Т80, при которой снижается объем жидкости гидроразрыва до 2-4 м с одновременным увеличением проппаната до 20 т и более. Осаждение проппоната на конце трещины препятствует увеличению длины трещины. При дальнейшей закачке жидкости, содержащей проппонат, происходит увеличение ширины трещины.
На основании проведения опытно-промышленных работ выявлено, что в пластах с проницаемостью 0,01-0,05 мкм
2 оптимальная длина закрепленной трещины обычно составляет 40-60 м. Установлено, что увеличение длины закрепленной трещины не приводит к увеличению дебита скважины.
Основным оператором по проведению ГРП по данной технологии является Нижневартовское ЗАО СП «МеКаМи-нефть». Совместное российско-германо-бельгийское предприятие, появившееся на рынке технологий в 1992 году, имеет на счету не одну тысячу подобных успешных операций.
2) Гидравлический разрыв пласта с предварительной гидропескоструйной перфорацией:
С целью снижения давления гидравлического разрыва пласта и обеспечения направления образования трещин перед процессом гидравлического разрыва пласта осуществляют пескоструйную перфорацию. Как правило, проводят щелевую пескоструйную перфорацию. Для этой цели используют специальное оборудование, обеспечивающее создание в обсадной колонне и породе пласта выработок в форме щелей. Последующий гидроразрыв пласта производится по обычной технологической схеме, принятой для конкретных геологических условий и месторождений.
Как показывает практика, по преобладающей части скважин дебит жидкости увеличился более чем в 4–5 раз, дают нефти – почти в 4 раза больше.
3) Направленный гидравлический разрыв пласта:
Для повышения эффективности процесса ГРП важным является обеспечение заданного направления и пространственной конфигурации создаваемых в пласте трещин. В результате теоретических исследований отмечается, что для того чтобы в нефтенасыщенном пласте под действием фильтрующейся жидкости начала образовываться горизонтальная трещина, необходимо преодолеть вертикальное горное давление. Для того же чтобы начала образовываться вертикальная трещина, необходимо, чтобы давление жидкости превзошло боковую составляющую горного давления. Давление начала образования горизонтальной трещины не зависит от величины пластового давления, в то время как давление начала образования вертикальной трещины зависит от величины пластового давления. Однако на сегодняшний день нет надежной технологии, обеспечивающей заданную пространственную конфигурацию расположения трещин при осуществлении процесса ГРП.
В связи с этим в научно-техническом кооперативном центре Нефтегазтехнология при бывшем МИНГе проведены исследования по созданию технологии процесса ГРП с обеспечением заданного направления и пространственной ориентации образующейся трещины.
Суть предлагаемого способа заключается в создании в присква- жинной зоне пласта выработки определенных размеров и пространственного положения, что обеспечивает в дальнейшем заданную.
Метод заключается в осуществлении гидроразрыва пласта с проведением предварительной вертикальной щелевой разгрузки пласта тем или иным доступным в данных условиях методом. Метод может примется для интенсификации притока пластовых флюидов к скважине. Возможно применение метода как самостоятельно, так и в сочетании с другими методами улучшения фильтрационных свойств породы – коллектора в прискважинной зоне пласта.
Особенно эффективно применение метода на объектах, где, по данным промысловой практики, другие методы интенсификации притока не дают возможности значительно увеличить продуктивность скважин.
2.3.Технология одновременно-раздельной эксплуатации
Одновременно–раздельная эксплуатация скважин– совместная эксплуатация двух и более продуктивных пластов одной скважины. Применяется при добыче нефи (газа), а так же для закачки воды – при заводнении нефтяных пластов, рабочих агентов — для повышения нефтеотдачи и конденсатоотдачи, газа — в процессе создания подземных хранилищ газа и др.
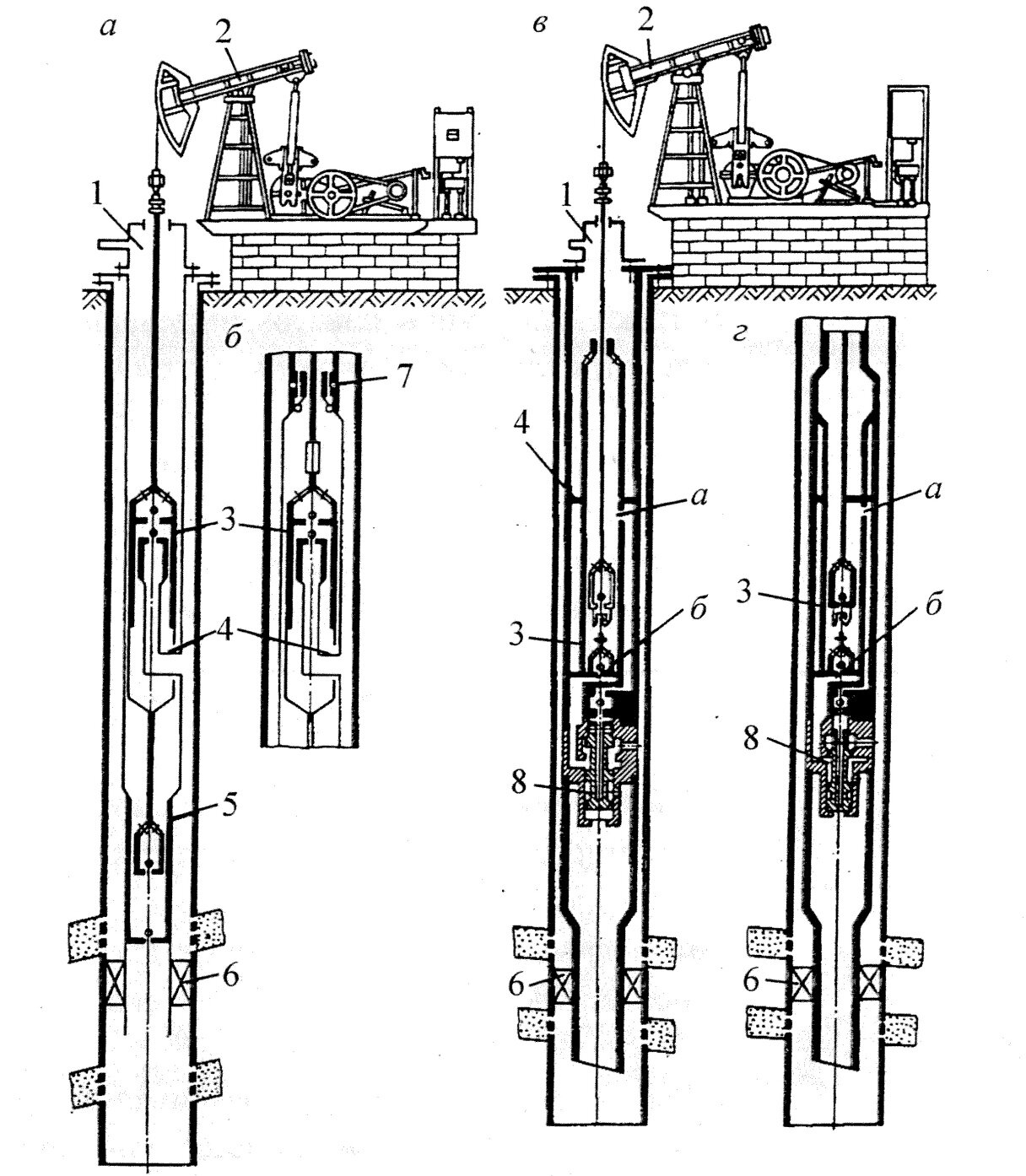
Рисунок 5 Установки для одновременной раздельной добычи нефти из двух пластов:
а) УГР вставного исполнения; б)УГР невставного исполнения; в) 1УНР вставного исполнения; г) 1УНР невставного исполнения:
1-оборудование устья;2-станок-качалка;3-верхний насос;4- опора; 5-нижний насос;6-пакер ПН-ЯМ;7-автосцеп 4АШ; 8-автоматический переключатель пластов.
Одновременно–раздельная эксплуатация (ОРЭ) применяется с целью повышения технико-экономической эффективности разработки за счет совмещения эксплуатационных объектов и осуществления при этом посредством специального оборудования контроля и регулирования процесса отбора запасов отдельно по каждому объекту.
Задачи, стоящие перед ОРЭ:
- повысить нефтеотдачу и дебит скважины за счет дополнительного вовлечения в разработку низкопроницаемых прослоев;
- увеличить степень охвата и интенсивность освоения многопластового месторождения, путем раздельного вовлечения в разработку отдельных тонких разнопроницаемых пластов-прослоев;
- сократить капитальные вложения на бурение скважин;
- интенсифицировать процесс регулирования отборов и закачки во времени и по разрезу скважины;
- увеличить рентабельный срок разработки месторождения;
- снизить эксплуатационные затраты;
- обеспечить учет добываемой продукции из каждого пласта и закачиваемого в него рабочего агента;
- оперативно управлять полем пластовых давлений, регулировать направления и скорости фильтрации пластовых флюидов.
Суть процесса:
В скважину спускают специальное оборудование (установки), обеспечивающие транспортирование продукции каждого пласта на поверхность (или закачку с поверхности в каждый пласт) по самостоятельным (или совместному) каналам, независимое регулирование и отработку пластов, а также проведение исследований, операций по освоению и глушению каждого пласта, технологическое воздействие на его призабойную зону. Одновременно-раздельная эксплуатация скважины позволяет сократить затраты на разбуривание, обустройство и эксплуатацию месторождений. Технологические схемы одновременно-раздельной эксплуатации скважины классифицируют по количеству эксплуатируемых пластов; установки одновременно-раздельной эксплуатации скважины по конструктивному оформлению; с концентрическими, параллельными и одноколонными рядами насосно-компрессорных труб (HKT), а также с регулированием отбора или закачки продукции по каждому пласту. Условия эксплуатации (величина газового фактора, содержание газового конденсата, уровень пластовых давлений и температур, состав добываемой или закачиваемой продукции, наличие агрессивных примесей, песка, парафина, минеральных солей и т.д.) влияют на конструктивные особенности установок и технологические схемы одновременно-раздельной эксплуатации скважины.
ТИПЫ ОРЭ
- Установка для одновременно-раздельной эксплуатации двух объектов (УОРЭ-146 (168).
- Установка для одновременно-раздельной эксплуатации двух объектов с раздельным подъёмом продукции (УОРЭ РПП-146(168).
- Установка для одновременно-раздельной эксплуатации двух объектов совмещающая добычу с заводнением (УОРЭ ДЗ-146(168).
- Установка для одновременно-раздельной эксплуатации двух объектов в скважинах оборудованных ЭЦН (УОРЭ ЭЦН -146(168).
- Установка для одновременно-раздельного заводнения двух объектов (УОРЗ -146(168)
Таблица 1 Показатели внедрения установок
№ п/п
|
Конструкции ОРЭ
|
ΔQн. Σ, тн.
|
Δqн, т/сут.
|
кол-во скв.
|
кол-во ПРС
|
1.
|
Однолифтовая |
743320
|
3,8
|
359
|
191
|
2.
|
Двухлифтовая с э/к168 мм |
237539
|
3,2
|
103
|
48
|
3.
|
Двухлифтовая с э/к146 мм |
28011
|
3,0
|
12
|
10
|
4.
|
Двухлифтовая добыча-закачка |
42643
|
4,6
|
29
|
15
|
5.
|
ЭЦН + ШГН с раздельным
подъёмом |
4044
|
2,4
|
5
|
11
|
6.
|
ЭЦН + ШГН со смешением
продукции |
70488
|
5,4
|
43
|
19
|
7.
|
С дифференциальным насосом
(полые штанги) |
3368
|
4,5
|
4
|
1
|
8.
|
С разделительным поршнем
(полые штанги) |
1140
|
2,8
|
2
|
-
|
9.
|
ЭВН + ШГН со смешением
продукции |
1209
|
3,8
|
3
|
1
|
10.
|
УВШН + УВШН со смешением
продукции |
151
|
3,9
|
1
|
-
|
|
Итого по всем конструкциям |
1131913
|
3,7
|
564
|
296
|
К преимуществам ОРЭ относятся:
- Возможность сокращения объемов бурения на многопластовом месторождении в среднем в 2.2 раза за счет использования ствола одной скважины и организации одновременного (совместного) отбора запасов углеводородов разных объектов разработки одной сеткой скважин.
- Снижение эксплуатационных расходов на удельную добычу нефти в 1.7 раз
- Сокращение потерь добычи нефти на период исследований (10 тыс.т на тысячу скважин)
- Обеспечение раздельного мониторинга добычи пластов (важно для достижения равномерности выработки залежей)
- Эксплуатация одновременно объектов с разными коллекторскими характеристиками и свойствами нефтей.
Повышение рентабельности отдельных скважин за счет подключения других объектов разработки или разных по свойствам пластов одного объекта разработки.
Описание однолифтовой установки для ОРЭ:
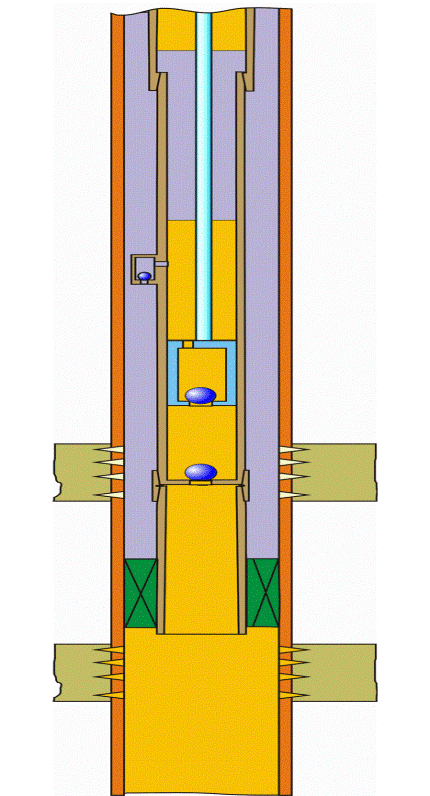
Рисунок 6 Однолифтовая установка для ОРЭ
Установка содержит штанговый насос с двумя всасывающими клапанами - основным и дополнительным боковым, каждый из которых сообщается с одним из двух разделённых пакером пластов. Продукция из пласта с меньшим динамическим уровнем поступает в цилиндр насоса через основной всасывающий клапан, а с большим – через дополнительный.
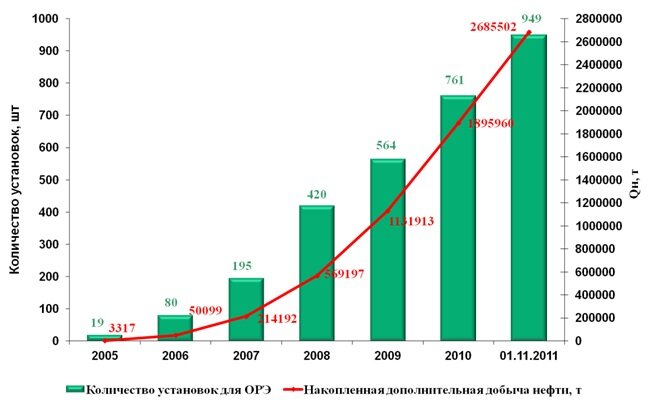
Рисунок 7 Динамика внедрения установок для ОРЭ и накопленной дополнительной добычи нефти
Установки для ОРЗ на 1.11.2011г. внедрены в 300 скважинах, общий объем закачки по подключенным пластам составил 7,79 тыс. м
3 воды, а дополнительная добыча нефти по реагирующим добывающим скважинам – 569,69 тыс.т.
Заключение:
- Технология ОРЭ имеет большое количество преимуществ, ключевая из которых в уменьшении сеток бурения и обеспечение оптимальной разработки пластов
- С приближением к максимальному разделению добычи, возрастает сложность технологий и их стоимость
- Существует большой спектр технологий и сформированный рынок услуг в России. При этом универсальной системы ОРЭ на сегодня нет
- Необходима разработка стандартизации подходов при выборе технологий ОРЭ, структурированности пилотных проектов и поступательного согласованного движения вперед на уровне компании
- Для увеличения наработки на отказ оборудования и увеличения ответственности у Поставщика, рассмотреть схему проката оборудования
4 Инновационные технологии для повышения эффективности использования углеводородов
4.1.Технология глубокой переработки углеводородов
Предлагаемая технология глубокой переработки нефти и любого другого углеводородного сырья позволит получать огромную дополнительную ежегодную прибыль и экономить сотни и тысячи миллионов тонн сырья. Другими словами, ее внедрение эквивалентно увеличению мировых запасов углеводородов в несколько раз.
В настоящее время наиболее широко распространены каталитические процессы углубленной переработки углеводородного сырья, однако даже они не могут предложить достаточно привлекательный технико-экономический баланс для многих нефтепереработчиков при переработке самых тяжелых видов сырья.
Более того, с помощью известных и широко применяемых каталитических технологий невозможно в принципе решить задачу 100% глубины переработки, т.к. тяжелые нефтяные остатки будут очень быстро приводить к отравлению и коксованию активной поверхности любого катализатора. Из-за высокого содержания в сырье металлов, асфальтенов наряду с сернистыми, азотистыми соединениями и другими вредными примесями и компонентами, происходит быстрая дезактивация катализаторов, закрываются поры, поверхность катализатора покрывается смолистыми и коксовыми отложениями. Все это существенно снижает селективность и эффективность классического каталитического процесса. Необходимость постоянного изготовления и обновления катализаторов, оперативная их смена и утилизация требует дополнительных капитальных и эксплуатационных затрат и повышает себестоимость процесса переработки и получаемой продукции.
Поэтому глубокая переработка нефти и нефтяных остатков, вовлечение в традиционную переработку газообразных и особенно твердых углеводородов является основной задачей ближайшего времени. Для решения вопроса глубокой переработки, рационального и экономного использования любого углеводородного сырья необходимо не просто улучшать известные углубляющие процессы (термический и каталитический крекинг), а изменить отношение к существующим технологиям нефтепереработки. Необходимо разработать новый подход или новое направление глубокой переработки углеводородного сырья, которое позволит осуществить безостаточную, практически 100% конверсию любого углеводородного сырья (жидкого, твердого, газообразного) в целевые легкие углеводороды.
Основное отличие и преимущество предлагаемого подхода и технологии заключается в том, что сырье, в основном тяжелое и содержащее большое количество разнообразных вредных примесей, непосредственно с катализатором не контактирует.
Сначала сырье подвергают мягкому некаталитическому (например, термическому и/или термомеханическому) крекингу.
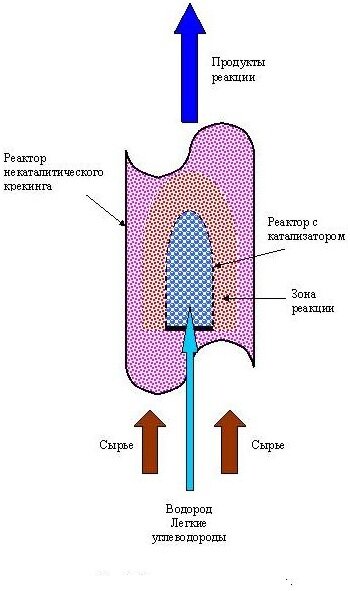
Рисунок 8 Упрощенная схема процесса
В процессе крекинга сырья образуются непредельные углеводороды, которые впоследствии могут конденсироваться, что приводит к ограничению глубины переработки. Для наиболее полной и глубокой переработки и увеличения выхода легких целевых продуктов и фракций схема переработки должна быть дополнена устройством, которое позволяет с минимальными затратами насыщать открытые связи атомарным водородом и/или легкими радикалами. Проблему можно решить такой организацией схемы процесса, при которой тяжелое сырье, содержащее вредные примеси и компоненты, и катализатор не контактируют, вследствие чего катализатор практически не отравляется вредными примесями и не коксуется, что приводит к увеличению долговечности катализатора и отсутствию необходимости его регенерации и замены. Для этого молекулярный водород и/или легкие водородсодержащие среды, обогащенные водородом (они не содержат смол, асфальтенов и других вредных примесей и компонентов), например, попутный, природный газ, в том числе газ и часть легких фракций, получаемых в процессе переработки углеводородного сырья, при необходимости подогревают (особенно для легких жидких фракций, получая из них углеводородный пар) и направляют для получения активного атомарного водорода и/или легких радикалов в реактор с нагретым до необходимой температуры катализатором (блок получения атомарного водорода и/или легких радикалов). Полученные активный водород и/или легкие радикалы направляют в устройства нагрева (учитывая высокую реакционную способность атомарного водорода и/или легких радикалов, которые являются своеобразными катализаторами) и/или некаталитического крекинга жидкого исходного сырья для проведения реакции (процесс схематически изображен на рисунок 8).
Нагрев водорода и/или легких водородсодержащих сред, обогащенных водородом, а также реактора с катализатором можно осуществлять за счет тепла нагретого сырья и/или тяжелых фракций, направляемых на повторную обработку. Давление в реакторе с катализатором должно быть больше давления в реакторе некаталитического крекинга сырья. Атомарный водород и/или легкие радикалы насыщают открытые связи непредельных углеводородов с получением легких целевых фракций высокого качества. Легкие насыщенные продукты реакции непрерывно выводятся из процесса для получения легких целевых продуктов (сжиженного газа, бензина, реактивного, дизельного топлива, продуктов нефтехимии).При этом такие дорогие процессы, как гидроочистка, риформинг и т.д. в блоках получения легких товарных продуктов могут не использоваться, т.к. открытые связи радикалов крекинга сырья насыщаются до блока получения товарных продуктов, а регулировка свойств и состава получаемых фракций производится изменением режима и параметров процесса.
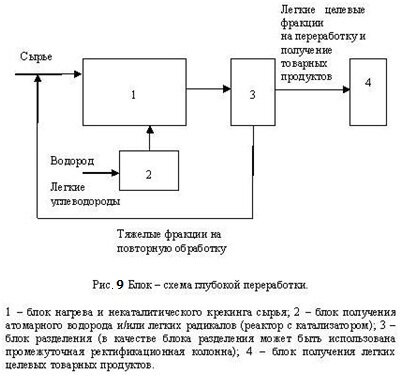
Кроме того, в процессе обработки сырья уменьшается количество вредных примесей, например сернистых соединений, т.к. в процессе обработки основная часть серы переходит в сероводород и далее выводится из процесса известными методами с дальнейшим получением, например, атомарной серы и других полезных побочных продуктов. Тяжелые фракции направляются на повторную обработку. При повторной обработки тяжелых фракций можно достичь практически 100% глубины переработки и выхода легких целевых продуктов. Непрореагировавшие молекулярный водород и/или легкие водородсодержащие среды, обогащенные водородом, могут возвращаться в начало процесса для повторного использования. При необходимости, тяжелые фракции частично могут направляться и для получения тяжелых товарных продуктов (битума, кокса и других). Укрупненная блок – схема процесса показана на рисунок 9.
Если получение молекулярного водорода в настоящее время является довольно дорогим процессом, то использование для получения атомарного водорода и/или легких радикалов природного или попутного газа, который во многих случаях сжигается на факелах, позволяет свести затраты на проведение процесса глубокой переработки к минимуму.
Технология апробирована на небольшой лабораторной установке. Глубина переработки достигает 97ч98%. С учетом образующихся несконденсированных газов, можно уверенно говорить практически о 100% глубине переработки сырья с помощью предлагаемой технологии.
Твердое углеводородное сырье (например, уголь, сланец, продукты растительного происхождения) направляют в блок мелкодисперсного размельчения и вводят в исходное сырье и/или тяжелые фракции перед повторной обработкой или приводят в непосредственный контакт с легкими радикалами. Газообразные углеводороды также вводят в исходное сырье и/или тяжелые фракции перед их повторной обработкой. Жидкие, твердые и газообразные углеводороды могут обрабатываться по данной схеме одновременно, по отдельности или попарно. Часть газообразных и/или легких продуктов (они обогащены водородом и могут заменять исходные водородсодержащие среды) переработки по данной схеме может быть возвращена в начало процесса в реактор с катализатором для получения активного атомарного водорода и/или легких радикалов.
Тяжелое сырье не вступает в непосредственный контакт с катализатором, не происходит его отравление и коксование, отпадает необходимость регенерации и замены катализатора, процесс упрощается и становится более надежным, стоимость процесса и оборудования значительно уменьшается, т.е. происходит снижение капитальных и эксплуатационных затрат, глубина переработки может быть увеличена до 100%. При этом происходит экономия сырья при выработке необходимого количества целевых товарных продуктов, другими словами оптимальное и рациональное использование сырьевых ресурсов при их дальнейшей переработке при реализации данной схемы. Кроме того, различные остатки и отходы, накапливающиеся в процессе, например, добычи и переработки нефти, приводят к ухудшению экологической обстановки, и их переработка по данной схеме с получением высоколиквидной продукции позволяет решать экологические проблемы и получать дополнительную прибыль. Минимальная производительность, при которой процесс становиться окупаемым, в несколько раз меньше, чем при использовании известных каталитических технологий. Появляется возможность строительства небольших перерабатывающих производств, непосредственно приближенных к потребителю и оптимально удовлетворяющих его требованиям.
Широкое промышленное внедрение предлагаемой новой экономичной, экологичной и эффективной технологии глубокой переработки нефти и любого другого углеводородного сырья по топливному варианту и производству продуктов нефтехимии позволит получать огромную дополнительную ежегодную прибыль и экономить сотни и тысячи миллионов тонн сырья ежегодно при полном удовлетворении рынка качественными горюче – смазочными материалами в полном объеме. Другими словами, внедрение таких технологий эквивалентно увеличению мировых запасов углеводородов в несколько раз без затрат на их разведку и добычу при существенном снижении стоимости готовой продукции переработки.
Разработка, возможно в кооперации с ведущими мировыми нефтяными компаниями, промышленных установок нового типа и модернизация всей нефтеперерабатывающей, газовой и угольной промышленности позволит увеличить занятость трудоспособного населения, оживит экономику, приведет к стабилизации мировой энергетической системы и скорейшему выходу из мирового экономического кризиса.
5 Заключение
В ходе работы были рассмотрены новейшие технологии и разработки в области нефтепромыслового дела. Были изучены технологии, влияющие на эффективную добычу нефти, интенсификацию притока углеводородов из пласта и технологии по глубокой переработки нефти.
В результате можно сделать вывод, что внедрение инновационных технологий в производство не только необходимо, при нынешнем технологическом прогрессе, но и рентабельно. Рентабельность – всегда была одной из ключевых позиций при внедрении новых технологий, как для собственников, так и для инвесторов. Новые технологии позволят получать огромную дополнительную ежегодную прибыль и экономить сотни и тысячи миллионов тонн сырья, за счет увеличения коэффициента извлечения нефти (КИН). Другими словами, внедрение новых технологий эквивалентно увеличению мировых запасов углеводородов в несколько раз.